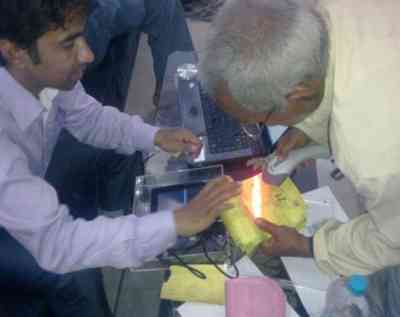
e-PDS Solution
The e-PDS solution is one of the most advanced systems of its kind in India. It is based on the systems integration and software technologies. The key objectives of the project were:
- Reduce or completely remove manual entries, exchange and records of data.
- Diminish and ultimately eliminate theft during transportation of grains.
- Ensure that SFC receives the dispatched weight of commodities from FCI without any pilferage.
- Ensure that FPS receives the allotted weight of commodities from SFC without any pilferage.
- Ensure that the FPS sells allotted commodities to consumers and does not black market them.
- Make the process efficient and effective by introducing process re-engineering and automation.
- Enhance oversight and monitoring through publishing of a variety of reports online.
- Introduce traceability and accountability in the system through effective alerts & notifications.
- Provide transparent and responsive system through public portal and information system.
These objectives acted as the key drivers in the architecting, design and development of the system. The automated flow and representation of data has been developed, keeping in mind the fulfillment of these objectives and exceeding these requirements if possible.
Front-end development essentially focuses and works on the visual perceptions of a website. It’s about the look, load time, pattern and functionality of the components of a website. Front-End is a mix of programming and layout that powers the visuals and interactions on the web. The talented Front-end developers provide turnkey Front-End development services whether you are planning to change the Front-End from older technology to newer one, for example Angular.
“I cannot give you the formula for success, but I can give you the formula for failure.
It is: Try to please everybody.”
– Herbert Bayard Swope
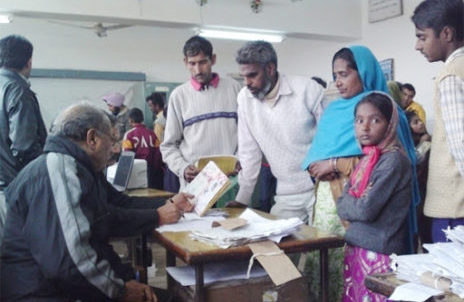
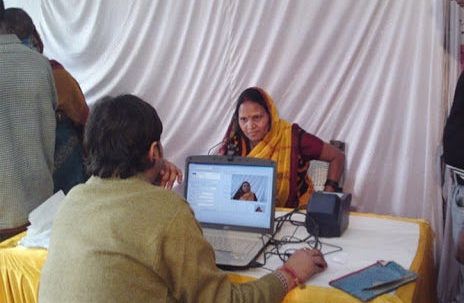
Process & Results
These objectives acted as the key drivers in the architecting, design and development of the system. The automated flow and representation of data has been developed, keeping in mind the fulfillment of these objectives and exceeding these requirements if possible.
To achieve the above listed objectives, a number of system components were developed which were loosely coupled but tightly bound to create a unified system of independent components. These system components are:
- Management Information System (MIS) at Head Office (Data Center)
- Advanced Weighing Stations at FCI and SFC warehouses
- GPS Tracking System for fleet of trucks
- SMS and Mobile based alerts notification system
- Point-of-Sale Terminal Retailing at FPS
These systems are explained briefly one-by-one in the next section.
- State-of-the-art Management Information System (MIS)
A data center has been established for the purpose of managing the e-PDS system. Servers based at this Head Office host and maintain the e-PDS application. The e-PDS application has the following modules:
- e-PDS Website
- General information, updates, photo gallery, government notices etc
- Citizen’s Portal with advanced grievance management system, FAQ, list of APL/BPL etc
- PDS performance reports for everyone to view online
- e-PDS Online Application
- Custom user pages for District Manager, District Supply Officer, District Magistrate, Marketing Officer and Assistant Godown Manager
- Daily activity updates and reports in detail, composite and summary form
- Methodical reports in statistical and graphical format for gap analysis
- Custom settable targets and goals
- SMS, E-mail and web/mobile based alert notifications for incidents reporting
- GPS Tracking System
All trucks ferrying food grains between FCI and SFC warehouses have been fitted with GPS-GPRS tracking devices in a ruggedized automotive class case, fitted inside the truck. The GPS transmits the location of the truck in real-time over GPRS to the central servers, which allow the GPS tracking application to perform the following:
- Plan route for each truck and save it by entering source, via points and destination.
- Once tracking is activated, trace the planned route vs. actual route taken by the truck on Google Maps.
- Flag any violations of diversion of route or undue stoppage on the maps.
- Send SMS based alerts and email/mobile based notifications to officials.
- Allow real-time monitoring of 100s of trucks on huge displays at the data center.
The GPS devices installed on the trucks are not ordinary devices available in the market. Rather, these are custom devices that have the following features:
- High sensitivity SiRF Star 3 architecture receiver with inbuilt GPRS on single chip from Telit™ with small antenna without wire.
- RFID Tag for radio frequency identification of vehicles at source/destination automatically.
- Small inbuilt solar panel with battery for power, requiring no external power.
- Hardened IP65 all weather aluminum enclosure that is soldered to a steel base to be soldered to the truck’s roof or over the top of it.
- Anti-tempering design that doesn’t allow the GPS device to be tampered with without complete destruction.
- Optional camera for snap-shot taking or video surveillance.
- Optional Microphone and Speaker to allow communication with driver.
The GPS device is unique in its design. It is required to be exposed rather than concealed like other GPS devices. Due to its self-powering and high-sensitivity receiver capabilities, it has no wires and is housed in an anti-tamper package, making any kind of tampering impossible except destruction. Again, due to its steel base, it is soldered either inside the truck upside-down on the roof or over the top of the roof of the truck. If the device is unsoldered, it automatically sends an SMS of tampering to the central servers with the ID of the truck.
Optionally, video surveillance is also provided. Based on specific triggers like diversion or undue stoppage, video recording can automatically initiate on store on SD card within the GPS device. The camera mounted on the back of the device records video that overlooks the storage space of the truck and any diversion or theft can be recorded in this way and retrieved later when required.
This fool-proof design ensures that once the GPS device is installed on the truck; it will always be tracked leaving no gaps or chances for truck drivers or others to tamper with and escape from being tracked.
Fig. 2 – Solar Powered Wireless GPS Device
- Advanced Weighing Station
The advanced weighing station is a system platform where Electronic Weigh Bridges and Electronic Floor scales have been installed at FCI and SFC warehouses. The weight of the commodities on these machines is directly recorded by an Advanced Weighing Station Panel.
The advanced weighing station panel is an electronic device that directly receives data from the electronic weigh bridge over an RF interface like Zigbee™ or Wi-Fi standard or through USB/RS-232 wired interface.
The advanced weighing station panel is housed in an all-weather IP65 aluminum enclosure and placed at an angle at the front or side of the weigh bridge.
The advanced weighing station panel has the following electronic interfaces serving a variety of purposes:
- Large 15 inch touch screen panel for display of vehicle registration number, weight and other details and touch screen allowing settings and configuration to the panel PC.
- RFID interface for automatically identifying the vehicles.
- USB/RS-232 wired or Zigbee™/Wi-Fi interface for fetching data from weigh bridge.
- Inbuilt Hi-resolution camera for taking vehicle snapshot when weight is fetched.
- GPRS connectivity for live data transfer to central servers with offline recording and timely online syncing of data.
- Thermal Printer for printing gate-pass, delivery receipt or challan.
- Contact/Contactless Smartcard interface for dealers for their identification.
- Standard 1D Barcode reader external attachment over USB to scan SIO.
- Solar Panel and sufficient power pack to power it as well as the electronic weigh bridge through power outlet or any other device.
- Optional Video Streaming for site monitoring and numeric keypad to enter weight if the weigh bridge is not electronic.
A software utility was developed in the system to perform the automatic task of identifying the vehicles, weighing them, issuing challan/receipts/gate pass etc and transferring the data to central servers.
The sequence of activities for this device at FCI is:
- Truck arrives and drives over the weigh bridge.
- RFID transceiver on the panel interacts with the RFID tag in the GPS of the truck and identifies it. The registration number of the truck is displayed on the LCD display after identification.
- Trucks driver or MO will simply press the “weight” button. The dry weight of the truck is automatically fetched and stored in the panel.
- After the truck is loaded with commodities, it arrives again at the weigh bridge.
- The panel again identifies and displays the registration number and also the dry weight of the truck. Truck driver or MO again press “weight” button. The loaded weight of the truck is displayed along with the weight of commodities, which is equal to the loaded weight minus the dry weight and weight of the sacks.
- A gate-pass is printed by the thermal printer and the truck leaves FCI.
The sequence of activities for this device at SFC is:
- Truck arrives and drives over the weigh bridge.
- RFID transceiver on the panel interacts with the RFID tag in the GPS of the truck and identifies it. The registration number of the truck is displayed on the LCD display after identification along with the expected weight of the commodities.
- Trucks driver or MO will simply press the “weight” button. The weight of the truck is automatically fetched and the weight of the commodities is displayed.
- A challan is printed in case the weight of the received commodities is less than the weight of the dispatched commodities. The information of the challan is also sent to the central servers for theft reporting.
In case it is a dealer’s vehicle to take its allotment, the sequence of activities is slightly different.
- Dealer inserts smartcard in the panel or the dealer’s SIO is scanned by a barcode scanner.
- This identifies the dealer and its ID is displayed on the display panel.
- Dealer’s vehicle is parked on the weigh bridge and its dry weight is fetched by pressing “weight” button.
- After the commodities are loaded to the dealer’s vehicle, the dealer again identifies itself through smart card or SIO and again parks its vehicle on the weigh bridge and presses “weight” button.
- The weight of commodities is calculated and a receipt is printed for the same.
In this fashion, vehicles are weighted automatically without manual intervention. There is no need for an operator as only pressing a button is required. The solution powers itself and also powers the weigh bridge through an inbuilt solar power system. Hence the solution is completely standalone.
Fig. 3 – Advanced Weighing Station Panel
- SMS and Mobile based alerts and notifications
Incident reporting and issue escalation is maintained by the MIS through an alerts and notifications system. The system keeps track of data on which trigger has been and automatically sends out custom messages as alerts through either SMS or email to officials in order to inform them of situations immediately.
Android based widgets and application has also been developed which can be installed in Android phones or tablets. This mobile/tablet application allows total oversight report viewing to officials while they are on the move. The following are the high-lights of the system:
- SMS/email alerts for diversion of trucks being tracked by GPS.
- GPS tracking map view on android phones/tablets.
- SMS/email alert to consumers who register complaints with the e-PDS portal to inform them of its status.
- SMS alert to Village Vigilance Committee heads to inform them of allotment of grains to FPS in their Panchayat.
- SMS/email alerts and notifications on custom triggers like distribution target, sales target, procurement target etc
- Point-of-Sale Terminals at FPS for Retailing
At the fair price shops, point-of-sale terminals have been installed to record sales done by dealers to consumers. Each POS is enabled with a barcode scanner to scan beneficiary coupons and GPRS connectivity to upload the sales transaction to the central servers. The POS has a custom developed application to sell grains and kerosene to consumers. The following are the highlights of the system.
- Local database of consumers on POS to allow offline transacting capability.
- GPRS syncs all transactions when it has connectivity available.
- Barcode scanning opens the profile of the beneficiary. Dealer only needs to add quantities for Rice, Wheat and Kerosene.
- POS speaks out in Hindi the details of transaction and a receipt is printed and issued.
- Small solar charger with light provided to charge the POS, all in one handy baggage.
This section explains the flow of the e-PDS solution and illustrates how each of the system components described above are utilized by different stake-holders.
Management Information System (MIS)
A Management Information System (MIS) has been developed to completely automate all processes of the PDS starting from the FCI till the FPS, which were executed manually. The MIS has been deployed on servers located at the Data Center. The MIS is the backbone of the e-PDS solution. It holds the data of each transaction and activity happening at each node of the e-PDS supply chain.
The key users of this MIS are:
- Advanced Weighing Station at FCI
- Advanced Weighing Station at SFC
- District Manager, District Supply Officer and the District Magistrate
- Tele-Support Executives at Data Center
- Project Manager/Administrator at Data Center
- Consumers
The following briefly explains how each of the above will use the MIS, as per the flow of the process.
At FCI, the MO will use the advanced weighing station. The Advanced Weighing Station software utility contains a local database of all trucks plying between the specific FCI and SFC. This detail includes the registration number of the truck, the transporter and other details of the trucks.
When a truck arrives to pick grains at FCI, the AWS will automatically identify the truck and where it is destined for. When processing has been done, the MO will press the option for “weight” of the truck to fetch the dry weight. The unloaded truck will park on the weighbridge and its unloaded weight will be fetched automatically.
The truck will then be allowed to move inside the FCI warehouse where it will be loaded with the required commodities. When the loading is done, the truck will be parked on the weigh bridge again and its loaded weight will be calculated by subtracting loaded weight with unloaded with to find the exact weight of the loaded commodities. A gate pass will be printed and provided to the truck driver.
The truck will leave FCI for the destined SFC warehouse. GPS tracking of the truck will start as soon as its gate pass is generated.
The routes between each FCI (source) and SFC (destination) warehouse are planned in advance including the “via points”, that is, the specific waypoints the truck has to go through for each truck lying between various FCI and SFC warehouses. Also set in advance are alerts for speed limit, stoppage time limit and diversion distance limit.
If the truck diverts from the planned route by a specified distance or stops at undesignated places, an SMS alert is sent to officials. On the live tracking being viewed on maps on display screen, such diversions are flagged and their detail mentioned.
When the truck is received at SFC, the AWS automatically identifies the truck and its profile along with commodity details opens up on the display panel. The truck is weighted and any differences between dispatched and arrived weight of quantities is considered theft. Theft is reported to officials and a challan is printed, which the MO or AGM can charge on the spot and an SMS alert is sent to the district manager and other concerned officials.
The GPS tracking for that truck will be closed and the route taken by the truck (route history) will also be saved in the database as “archived journey”.
The MO and AGM at SFC are also responsible for allocation of food grain to the fair price shops. When a dealer arrives at the SFC to receive its quota of grains, it first produces the Store Issue Order or SIO to the MO. Each dealer is provided with a smart card which it inserts into the AWS. The profile of the dealer and its allotment for the month appears, based on its sales registered for the previous month. Sales for the current month are also recorded for SIO generation for next month.
Based on the allotment, the dealer’s vehicle is weighted dry on the electronic weigh bridge. Afterwards, the allotted amount of grains is loaded onto its vehicle. After the loading, the dealer again inserts its smart card in the AWS and its vehicle is again weighted on the electronic weigh bridge and the weight of the commodities calculated by the software. The dealer takes its quota and its SIO is marked as closed and archived. The information is reported to the district manager.
The district managers, district supply officer and the district magistrate are responsible for the fair and free movement and sales of grains at SFC. The DM and DSO are provided with custom web pages which they can log in to and check reports, activity, etc and control theft and leakages through monitoring and oversight. Some of the reports are as below:
- Activity Reports
It contains the summary of food grain movement to and from SFC warehouse, theft reported, sales and current inventories. The activity report is generated daily. It can be viewed on current/date-wise basis, weekly/monthly/yearly basis.
- Theft Reports & Alerts
It contains the thefts reported. A list of theft alerts, the latest one being on the top, is displayed. Clicking on any of them provides a detailed theft report. These reports can be searched using a variety of search options like date, truck number, transporter, etc. Along with theft reports list, each report contains GPS option clicking which Journey taken by that truck can be viewed showing the planned route, actual route taken, alerts etc.
- Movement Reports (Grain Procurement, Sales & Inventory Reports)
The SFC grain procurement, sales and Inventory reports detail the exact procurement, sales and stocks in terms of commodity, type, scheme, quantity, etc. There are three buttons to choose from, each providing a list of reports. These three are the purchase reports, sales reports and the inventory reports. The procurement done by the SFC from FCI or sales done by the SFC to dealers is listed in “latest on top” fashion. Again, selecting any report will show the details of that purchase, sale, and inventory till date. The reports can be viewed based on filtering options that include viewing by date/commodity/type/scheme/etc. Graphical representations will also be shown like pie charts, bar graphs etc.
- Grievances
The grievances option shows the list of grievances with the latest ones being on top. Grievances can be searched based upon filtering options of date/complaint number/status/priority. The district manager or district supply officer have the right to enter comments on the grievance, change its priority and status and assign the said grievance to any official in the PDS. A superscripted number will show the current/pending number of complaints on the top of the grievance option button.
- Contacts
Contacts allow the officials to maintain the names, numbers, email IDs and address of government officials involved in the PDS. Upon searching or selecting a contact, potions are provided to allow emailing, calling and SMS-ing to that contact.
The datacenter has staff to support and manage the PDS operations. Tele-support executives are based at the data center which is equipped with state-of-the-art servers and networking infrastructure. Additionally, the data center has two dedicated internet lines and 2 phone numbers and a toll-free number for call center operations. The Tele-support executives help the electronic weigh bridge operators at the different centers with technical help and also liaison with district manager and district supply officer if need arises. The data center is also equipped with a 52” LCD screen on which each truck plying between FCI and SFC warehouses can be monitored. GPS tracking of trucks is displayed on this screen and any diversion or stoppage alerts can be viewed and officials alerted. The callers also call truck drivers in case they view a diversion so that it acts as a deterrent for the truckers from stealing.
The project manager is the primary person required to run all the data center operations successfully. Government officials can request the project manager for producing/presenting any data, current or archived. For example, the district manager, upon receiving information about theft, can request Tele-support executives at the data center to retrieve the GPS history of the truck and find out if the truck diverted to another route or stopped at unscheduled locations in order to find out probable theft spots.
The ultimate beneficiary of this system is the consumer. The web portal www.pdsonline.in is accessible to everyone on the internet. In the website, there is a “Citizen’s Portal”. The citizen’s portal is meant to provide citizens with information in order to make the system transparent and the officials accountable. Every citizen of India can register with the online portal. Upon registration, the user will be emailed a username and password. An SMS would be sent to the mobile number of the user that will confirm the registration of the user to the portal. Once the user is registered, he/she may enter the website using his/her username and password.
Upon login, the user is able to view “My Profile”, “Grievances” and a “Reports” menu. The “My Profile” menu contains the profile of the user along with his/her personal details which the user himself/herself can update. It also contains check-box options that a user can select to receive email or SMS alerts when the retailer he/she is attached to receives its allocation of grains from SFC. The user can use the “locate your fps” option to first search the FPS number relevant to him/her receive alerts accordingly.
The reports menu contains the summary reports of grain movement from FCI to SFC and from SFC to FPS. These reports can be filtered and viewed using multiple options. This automatically provides citizens with a tool to know and be informed about grain procurement and sales across the state. This is an automatic route to RTI. The reports are available without a login as well.
The grievance section of the portal is one of the most advanced and transparent grievance redressal systems available with any government of India website or department. The following are its key features:
- Register with the website and write a complaint in the grievance section. You can also attach files including audio/video as evidence or proof in case it is required, example, to report theft or black marketing.
- An SMS complaint can be sent by sending “pdscomplaint” as subject followed by the complaint to a long-code.
- An MMS complaint can be sent by sending “pdscomplaint” as subject followed by the complaint to the long code, including attaching Image/Audio/Video as evidence.
- Once the complaint is registered, an auto-generated complaint number is assigned to the user using which he/she can track his/her complaints.
- The best feature is that once a complaint has been registered, any action taken on it by any official, like assignment of complaint to another official, change of status, priority, official comments etc, an email/SMS alert is sent to the consumer with all of the above details, that is, status, assigned to, assigned by, date/time, resolution comments, etc. Hence, a user can figure out if any action is being taken on his/her complaint and who is handling the complaint and what resolution has been proposed for that complaint. This makes pdsonline.in armed with the most transparent and genuine grievance redressal mechanism across the government.
Fig. 2 – Grievance on Phone
Apart from the citizen’s portal, the website has a “Schemes” menu that contains all information about government schemes towards PDS. Also available is an “FAQ” section where all relevant questions pertaining to PDS are contained in Question and Answer format for easy understanding. All website interfaces are available in Hindi language as well.
Fig. 3: Flow of Food Grains from FCI to Consumer using the new system
There are numerous benefits of the solution described above. Some of them are:
- Provision of automation at each level of the PDS flow increasing efficiency.
- Minimal chance of mismanagement and cheating as manual intervention has been eliminated.
- Transparency in the system as all issue orders, arrival/dispatch reports, gate passes etc are generated automatically and transmitted electronically.
- Accountability in the system as food grain off take is authenticated from the consumer end and moving upwards till the FCI, encompassing the complete supply chain.
- Complete oversight to the District Manager’s office about the food grain movement starting from the FCI warehouses and ending with the consumer.
- The solution has automated most of the processes of the PDS and provided a state-of-the-art system, including but not limited to Electronic Weighing, Tablet based real-time data points to district officials, phone based applications and unparalleled access to information to the citizens.
- The solution is “UID Compatible” as Unique ID field already exists for consumer’s database and can be linked to aadhar based identification and if needed, authentication.
The following section details out the technologies that have been used in the implementation of the MIS. A brief about the software technologies that we utilized in the development of this MIS is provided below:
For implementing the database, SQL server 2008 R2 was used. There are various advantages of using SQL server. Some of them are:
- Scaling Out
For the MIS, a huge database needs to be created. Such a database will also be required to be scaled out. It will be required to add more consumers, SFCs, FPSs etc to our database and the scope of the implementation could go beyond the district in the future. SQL database is scalable and the database can be grown without inviting complexity.
- Provision of Linked Server
SQL server provides the facility of linked server by which we can easily fetch the records by combining any table in any of the databases. There could be instances when more concurrent requests may need to be processed than expected.
- Provision of Service Broker
SQL server provides what is known as a Service Broker. Service Broker can be used to handle asynchronous transaction processing, replication and more. The load on the application could raise or shrink dramatically. Hence, asynchronous transaction processing may be required.
- High Availability
A high-availability solution masks the effects of a hardware or software failure and maintains the availability of applications so that the perceived downtime for users is minimized. No user would like to wait; hence the system should be available even if it has to fetch millions of different user data simultaneously. In order to provide high availability, we will use database mirroring along with log shipping on our portioned database.
- Reliability
SQL server is widely used and is perceived as one of the most reliable database technology. It also goes well with applications developed in dot Net technology.
Reporting Service
We used SSRS (SQL Server Reporting Service) for report generation. SSRS is a fast stored procedure based reporting service which is built on the .net framework. The advantage of using SSRS is that it provides fast batch execution program, which helps query millions of records in few seconds. SSRS also provides business level graphs an excellent user interface and graphics for reports, improving the usability of the software application. SSRS will be deployed on the main database server that will provide fast execution of queries because of being on the same machine.
The main application has been developed on .NET 4.0 framework. The application is available through the internet to FCI warehouses and SFC warehouses. The application and the databases are hosted at servers based at the data center. The following technologies have been used to implement the web based application.
- Windows Presentation Foundation (WPF) has been used as it is state-of-the-art, takes minimal execution time and provides excellent graphical user interface.
- The core technology is .Net. It is the standard and de facto technology used today to create high productivity applications. It is easy to manage as well.
- For client server interface, we will have used Windows Communication Foundation (WCF) to create client-server architecture so that multiple clients can access the data from a centralized server. Remoting feature of WCF has been used to create Local Area Network (LAN) based application. WCF provides the easy migration from LAN Application to Internet based web application.
- A very huge advantage of using WCF is that we can use the parallel programming feature of .net to utilize the multicore processor in an efficient way. By making use of threading in parallel programming, very fast processing and access can be achieved in remoting.
- WCF 4 works on .net 4 platform, hence, future upgradation or enhancements could be easily taken care of, providing system scalability and enhancement opportunities.
A standalone process has been implemented for error handling in .Net 4.0. This process logs the errors in a text file with all the details of the error. This helps identify the error and debug them quickly. It also provides real-time firsthand information related to any errors that crop up in the application so that developers will be in a position to respond immediately and provide fixes in a very short turnaround time.
In this section, we define the software implementation details. We will explain how databases have been created and how the application has been developed module wise for each feature in the PDS solution.
The master information is stored physically on servers in the form of databases. Application interface allows users to access this information as per their role and access credentials. The following database has been implemented for the PDS solution:
This database contains the information of all employees who use the web based application at DMO, FCI and SFC. It contains the complete information about the employees like their names, addresses, contact info, etc and also their role specific information like their designation, their access and credentials to portal modules, etc.
Warehouse Data
The warehouse database contains information of each warehouse (FCI or SFC) in the district like warehouse ownership type, capacity, address, owner, GPS location etc.
The dealer database includes the details of each and every dealer in the district. The details include the name of the dealer, the location of the shop (address), its quota of grains, the SFC it is attached to and other relevant information.
The transporter database contains information about the transporters associated with the SFCs. It lists the transport companies, their owner information, and information of all trucks of the transporter associated with the SFCs etc.
The consumer database contains the details of all consumers in the district who possess APL, BPL etc cards and are entitled to subsidized grains from the government. Details like name, address, number of members in the family with their names, card type, quota etc is stored for each consumer. A field for UID is also contained which will be populated once UID is rolled out in these districts.
The web application has several modules which have been implemented to take care of different functional aspects of the PDS solution. The following modules have been developed:
- Website Management Module
- Grievance Management Module
- Enterprise Management Module
- User Management Module
- Consumer Management Module
- Geography Management Module
- Fleet Management Module
- Warehouse Management Module
- Financial Management Module
- Reports Generation Module
A brief description of each module is provided next.
A portal www.pdsonline.in has been developed for providing a public view to the new PDS. The website is available in both English and Hindi. It contains various pages like schemes, citizen’s portal, gallery, news, govt. orders and circulars, feedback etc. All these pages can be managed through the website management module.
The website management module provides a very easy to use interface to edit/remove existing content or add new content to specific pages like main page, News section, Govt. orders and circulars section, FAQs, Gallery etc. The interface is just like “facebook” where the website admin can simply login, edit/remove/add new text, style the text using a text editor, upload images/videos and archive older information. There is no need to change the source code of the website as no content is static or un-manageable.
Feedback received on the website is also manageable from website management menu. Feedback sent by the public can be viewed in a list fashion with the latest being on the top. Upon selecting, it can be viewed in detail.
The grievance management module has a public interface and an admin interface. The admin interface allows employees/internal users of the PDS system to assign specific grievances to officials like a district manager may assign a grievance to an AGM. It also allows the internal user to set priority of the complaint and change the status of the complaint. The internal users will write their comments against the complaint which will be visible to other internal users. Each action taken is time and username stamped. It also allows searching grievances by period, priority and status.
To the external user, which is the consumer, it allows raising a new grievance or viewing older grievance including the option to search grievance by specific code. The user can also view comments put by officials on his/her complaint but it does not allow the user to add more comments once his/her grievance has been submitted. The user receives an SMS/email alert after successful submission of the grievance and whenever there is any change in the status of the complaint, till it is resolved.
Fig. 4: Screenshot of the PDS Website
The Enterprise Management module contains the master information of the various parameters that form the fundamentals of the commodity economics. It manages information like commodity, commodity type, bag type, rates, scheme-wise allocation, scheme-wise rates, etc. The admin has access to this module and he/she can add/edit/remove the above mentioned data.
User management module is an admin module used to add employees/users of the online PDS system. The users do not contain consumers, but professional users only. These users include MO, AGM, DM, DSO, etc. The admin can add/edit/delete information of users. For each user, fields like name, address, contact info, designation, geography, etc is entered.
The consumer management module is an admin module. This module contains the database of all the consumers in the district. The consumer database for the district is based upon the FPS linking of each family. A blank field for UIDs also provided in the database in order to allow addition of UIDs in the future.
Admin can add/edit/delete names of consumers to the database. For each consumer, there are fields like name, address, number of members in the family, scheme applicable, quota, etc. When a consumer approaches the district head office to register a new BPL/APL card or add a member to the card, his/her records can be retrieved, reproduced or updated.
This module can be used to track consumer consumption of grains. All consumers are provided coupons by the district collectorate. These coupons are collected by the FPS on sales and then gathered and presented to the MO/AGM when the dealer collects his/her allocation of grains. All coupons are barcode scanned and the total sales of the FPS are calculated. In this fashion, the total sales and hence available allocation quota of the FPS is founded. The coupon bar-coding can also be mapped to individual consumers to find out which consumer has bought his/her quota of grains and such information could be utilized to figure out activity and sales on a unified consumer base.
This is also an admin module. The geography management module describes the geography of areas where PDS is required to operate. In order to manage the scope of operations of PDs in terms of district, block, panchayat, village, nagar, palika etc, geography management allows addition/update of areas under PDS. Hence, if the scope of services for the PDS is extended to other districts of the state, the current solution is deployment ready.
The fleet management module contains the details of the various transporters operating for PDS. These transporters have trucks pressed into service for grain movement for the government. The fleet management module consists of the name, address, company registration, year of operation, incident history etc of the transporter. Also included with each transporter is their geography of operation and trucks under their service. Again, details of the truck such as truck driver, truck number, truck model/year etc are also maintained.
Apart from transporter and truck management, the fleet management module includes GPS management. GPS devices can be registered and added with the MIS. Each of these devices is track ready. Once a new truck or an existing truck who’s GPS is damaged is required to be tagged with a GPS device, the GPS management simply allows mapping of any active GPS device to any registered truck in the MIS. Hence GPS portability, if required is also realized this way.
The fleet management module also contains two applications. These are the GPS Live Tracker and the GPS Archive Tracker. The GPS Live Tracker shows the tracking of independent trucks when they leave from FCI warehouse to a SFC warehouse. This tracking is live and is shown as it progresses. All alerts that are set are generated and reported in real-time through email/SMS. The tracking keeps happening till the truck delivers the grains at the destination. Once the journey is complete, the journey along with its history of alerts/messages is archived in the database. The archived journey can be viewed by using the Archived Truck Tracker application. User can enter specific period, truck number, transporter, source/destination, gate pass number etc and select the required journey from the filtered list of journeys and view it on the maps.
Warehouse management is also an admin module. In warehouse management, information about the various warehouses like name of the warehouse, name of the warehouse owner, address, warehouse type, warehouse capacity, number of sheds, shed capacity etc are recorded. Also recorded are the GPS coordinates of each warehouse.
Admin can add a new warehouse tagged to a specific geographic location. Admin may also remove or update any warehouse related information.
The financial management module contains all the sales and banking related information including but not limited to SIO Generation, SIO Validation, SIO Validity Extension, SIO Cancellation, Bank Draft entry, Bank Challan Entry form, Bank Reconciliation, Demurrage Debit Notes, Supplier Payment Voucher, item ledger and other banking reports.
It is planned that dealers will be able to order their supplies online using net-banking once the banks provide us with the APIs of their payment gateways. The payment gateway for food grain requisition and purchase would be provided in the financial management module only.
The reports generation module generates various reports required by different users of the portal. The report generation can be filtered according to time duration, source/destination, transporter/truck, commodity/type, etc., including multi-select option. Some of the reports generated are:
- Draft Bill Cum Transport Pass
- Final Bill cum Transport Pass
- FCI Sales Report
- SFC Procurement Report
- SFC Sales Report
- FPS Purchase Report
- Movement Report
- SFC Inventory Report
- Theft and Loss Report
Some local/PC applications were also developed for PDS. The following describes these applications and there usage:
As part of the turn-key IT solution, GPS has been installed on trucks plying between FCI warehouses and SFC warehouses. The GPS devices are equipped with GPRS connectivity that allows it to send the GPS location and other parameters directly to the servers using internet.
When a truck leaves an FCI warehouse, GPS tracking is activated once gatepass is printed at the FCI. The GPS coordinates, speed, time and direction are received through GPRS. Administrator can set limits for stoppage time, speed, diversion (in meters distance perpendicular to the track) and departure/arrival alerts. If a truck diverts by, say, 100 meters and diversion limit is set to 100 meters, then an SMS/email alert will be automatically generated and sent to the data center and also to the concerned officials. When a truck finally arrives at the destination SFC and the commodities unloaded, the “submit” button on the arrival form closes the tracking. The journey along with all alerts is saved as an archived journey.
At the data center, a 52” screen is installed where all the trucks are simultaneously viewable on the maps. All alerts corresponding to various trucks are shown as a lit against truck numbers and also as overlay on their routes on the map. A tiled view is also available for each truck on the road at that moment and clocking on that tile opens view for that particular truck on the maps. This application is installed locally on the servers of the data center. The combined view of all trucks is called “Fleet View” and the individual truck view is called “Vehicle View”.
Fig. 5 – Snapshot of GPS Truck Tracker
Viewing the live or archived journey for a single truck is also possible. It can be viewed by logging into the MIS its credentials are set so that select officials can view the journey. Only “Vehicle View” is accessible outside the data center through normal internet.
The administrator can add GPS devices to the MIS and map them to trucks. Source (FCI) and destination (SFC) coordinates are provided by the admin to the GPS application. Administrator can also add “via points” which are waypoints through which the trucks route is planned. These via points are fixed for each route and can be added or removed by the admin.
The most innovative part of the solution is providing PDS tracking and monitoring application to officials on smart phones and tablet PCs.
The application has already been discussed earlier in section 5.1.1. The district manager and the district supply officer are provided with an Android based tablet PC that is enclosed in a leather case with a keyboard. The same application can be downloaded and used on other tablets and smart phones including Iphone, Ipad, Android, Windows mobile, Blackberry etc.
The application provides extraordinary graphics and visuals in the form of widgets. The application can be launched from any of the above mentioned platforms. Once the application is launched, it provides the user with icons selecting which information relating to it is presented in list and graphical formats. Below is a snapshot of that application.
Fig. 6 – Reports on Mobile Phone
One excellent feature of the tablet/smart-phone solution the “Set Goals” feature. This feature is for high level officials like District Manager, District Supply Officer and District Magistrate. As these officials will not always have the time or opportunity to monitor the system, they can set goals/targets with metrics. Example, the district magistrate can set a goal to reduce the thefts to under 10 quintals daily and 250 quintals per month. If the numbers of thefts exceed that target, they will be notified by the application on the tablet/phone and will also get an email/SMS notifying inability to meet those targets. The officials in charge can set such targets and these targets will automatically be set for every one using phones/tablets and even for those using the MIS over internet.
Similarly, goals can be set for a variety of objectives like maintaining inventory, procurement and sales of grains etc. This greatly helps managing the affairs from the top without being unnecessarily flooded with alarms and information. It helps make sense of the system and track its performance and targets can be fine tuned with time once they are met. This also allows realizing the actual objectives of having a system in place.
Fig. 8 – Tablet PC with Icons for Reports
Sales to consumers at fair price shops were done manually till e-PDS. The ultimate goal of the PDS is to make sure subsidized grains reach the intended people. Hence, it is necessary that sales to consumers at FPS may be tracked.
Typical complaints by customers range from dealers not opening shops, declining request for grains by reporting shortages to black marketing of grains by FPS. Dealers often hoard their grains to sell them illegally when there is shortage of grains. They also sell the grains received by them illegally to middlemen. Often, authorized consumers are denied grains by dealers sighting lack of supplies.
Introduction of POS terminals changed the scene by providing the administration with the capability to track grain sales to consumers resulting in accountability and ultimately benefitting the consumer.
As already mentioned earlier, the consumer database created in the current solution is based upon the dealership to which they are attached. Therefore a relative database according to each FPS is maintained locally in a POS terminal. The POS terminal has the following features:
- Memory and computing resources to maintain and process sales to consumers, including relative database of the consumers under that FPS.
- GPRS connectivity to record sales to consumers directly over the servers at the data center when connectivity is available and record sales transactions off-line when connectivity is not available.
- Barcode reader to directly read coupons provided by consumer and self recognize/enter data for that customer/transaction.
- Screen with English/Hindi text and graphics to show commodities, rates, weight and total. Recorded audio to “speak out” commodity, its quantity, its rate and total amount loudly in English/Hindi.
- Provision of thermally printed receipts to consumer against the sales.
Fig 9: Screen for POS Application
The benefits of having a POS terminal at the FPS are many. First, helps maintain a record of all sales by the FPS to the consumer and directly record the transactions to the MIS through its web based interface. This does not allow the dealer to make unauthorized transactions as all its sales would be recorded automatically. Second, when the dealer goes to the SFC warehouse to procure his/her quota of grains, the officials at the warehouse can find out from the MIS how much grains the dealer had sold to the consumer. Hence, its quota of grains will equal its sales to consumers. Therefore, if a dealer is black-marketing grains or hoarding them, he will not be entitled to more grains and it could be caught and penalized. The POS can later use UID as an identity and UID of each consumer can be typed in the POS through which sales can then happen.
Fig 10: POS System
As a pilot initiative in Gaya district, the Government of Bihar along with district administration of Gaya undertook the tedious task of automating SIO process and bringing efficiency and efficacy in Store Issue Order generation and distribution.
The overall management and oversight was to be carried out at a centralized location from where the SIOs for Gaya district would be verified, generated and distributed. All data was required to be uploaded to a central database and multiple reports were required to be generated. The task also included process re-engineering to improve traceability and accountability.
A comprehensive SIO management software application was implemented that computerized and automated all aspects of SIO process and introduced process re-engineering to remove possibilities of manipulation and duplication. The application contained several modules which computerized the SIO process end-to-end, automating all possible tasks associated with requisition, verification, generation and distribution of SIO to dealers. The key features and functionalities are described next.
SIO Requisition
Manual Process
Earlier, the dealers used to collect food coupons from the beneficiary against their sales. These coupons were produced by the dealer to the MO as proof of sales to consumers. The MO was required to maintain a paper record of all dealers, manually calculate their sales and then create an allotment list. This allotment list was physically transported to the District Manager’s Office.
This approach, both slow and inefficient, also allowed resulted in inaccuracies and manipulation. Often, DMO did not receive allotment lists from MOs as they had to wait for a substantial number of dealers to bring coupons and prepare an allotment list accordingly, further adding to the delay.
Automated Process
In the automated process, the MO can add the details of coupons received from each dealer into an XLS sheet, which automatically calculates the allotment on the basis of coupon count as per scheme. The MO uploads the XLS through his custom web page on the MIS. Each sheet is saved with a new reference number and duplicate entries (entries available in previous sheets) are not repeated, creating an updated, unified list of all allotment entries.
This simplifies the allotment list creation task and speeds up the process. All data is recorded at centrally managed servers.
SIO Verification
Manual Process
The dealer used to be informed about its allotment details by the MO at the SFC. The dealer was next required to deposit the requisite amount with the bank, which provided the dealer with a pay-in slip. Dealers were required to provide pay-in slips to MO who used to confirm the payment against the allocation and send out the confirmed list to the District Manager’s Office for verification. The District Manager’s Office used to manually compare and verify the deposit (pay-in slip) against the details provided by the bank. Often, details from banks would arrive late. Verification was a tedious, painful and slow job to carry out.
Automated Process
The SIO verification process has been re-engineered and the depositors list and details are received from banks in a specifically formatted XLS Sheet at a specified frequency. These details are automatically uploaded to the SIO Verification Module where payment details for each dealer as provided by the bank are marked against the allocation list generated automatically from the SIO Requisition Module.
Dealers who deposit the appropriate amount against their allocation are automatically verified by the software. For dealers who deposited more than the appropriate amount, their amounts are adjusted automatically in the ledger. Dealers who deposited lesser amounts are flagged and they are informed by the MO to deposit more amounts in the bank or adjust the amounts of grains, the difference of which is adjusted in the subsequent month’s allocation.
The MO is allowed to view only, the status of SIO verification and accordingly inform the dealer about it. This process re-engineering has eliminated the chances of introduction of fake pay-in slips as allocation is now against the real deposit information received from the bank and not against the pay-in slip produced by the dealer. All verification tasks are automated resulting in speed-up, accuracy and efficiency.
SIO Generation & Printing
Manual Process
All verified SIOs were earlier required to be listed on paper and then manually created by writing details of the SIO on a pre-printed SIO. Hence, each SIO required substantial amount of time to be created.
Automated Process
After all requisitions for food grains have been verified automatically by the SIO verification module, SIO is required to be generated, printed and distributed. The SIO generation module picks up the list of verified SIOs and sends them to the district manager for approval. The approved SIOs, digitally signed by the District Manager, are sent as a print job to the printer, which is loaded with pre-printed SIO paper. Each color represents copy of the SIO for different stake holders. They are:
- One copy for the District Manager’s Office
- One copy for the AGM at SFC
- One copy for the MO at SFC
- One copy for the FPS Owner
The software automatically prints the details of SIO on these colored papers and prints 4 copies as described against each SIO. When all copies of an SIO are printed, the SIO is marked “printed”. The software and printer is capable of printing multiple SIOs in one go. On the average, up to 700 SIO are generated and printed daily.
As a value addition, a barcode has also been introduced in the SIO, which is printed by the software. When the dealer arrives with the SIO, the SIO is simply scanned by a barcode scanner and details of the dealer are automatically fetched. The sales of grains to the dealer are recorded against its profile with the centralized MIS and the same information is also tagged with the SIO list, finally closing the SIO and archiving it for reporting and record purposes.
SIO Reports
All information of SIO process, from the initial bank deposit by FPS till the reception of grains by the FPS are recorded on centralized database at the District Manager’s office. This allows generation and representation of sales, deposits, banking and other details in numeric and graphical forms of reporting.
Several kinds of reports can be generated using this module by utilizing simple filter options. Reports can be generated for:
- Dealer or Block or District wise SIO Summary
- Dealer or Block or District wise Banking Summary
- Dealer or Block or District wise Sales Summary
- Dealer or Block or District wise Composite Report
Benefits of SIO Automation
SIO automation in Gaya District has been successful in thoroughly speeding up the process of SIO verification, generation and distribution. It has also resulted in improved efficiency and efficacy. Some of the benefits are listed below:
- Removal of manual intervention, improving accuracy and eliminating manipulation in the whole process.
- Removal of bogus pay-in slips and hence SIO.
- Removal of dependencies of SIO process from many stake holders and converging overall process at a central location, resulting in enhanced control and oversight.
- Process oriented Information exchange between stake holders like Banks, FPS SFC and District Manager’s Office.
- Status information to dealers at SFC itself, who earlier used to run from pillar to post to get information about their SIO generation.
- Remarkable speeding up of SIO process. In just two months of SIO process automation, the SIO generation and distribution has covered a delay of last four months and is catching up with the current month.
- Multiple customized reports available to officials anytime on mouse click.
- FPS owner’s allocation related to actual sales to consumers by linking registration of food coupons to grain allotment.
Fig. 11 – SIO Generation Summary Report
Fig. 12 – Bank Deposit Report
Fig. 13 – Block wise SIO Generation Report
The implementation of the solution is expected to be done on “Build, Own, Operate and Transfer” or BOOT model. Oglacs will completely build the system including development and maintenance of software, procure & install/commission hardware, setup and operate the data center, provide equipment and services on the field and maintain the solution for a fixed term based on contractual agreement. After the expiry of the contractual duration, the solution and assets will be transferred to the government completely including all hardware, software, source codes, blueprints, etc.
For the deployment of the proposed solution on BOOT basis, the following needs to be specified:
- Scope of deployment
- Scope of activities to be undertaken by Oglacs
- Provisions required from the government
- Deployment Schedule
- Main Business Objectives and Key Performance Indicators Scope of deployment
The proposed solution is expected to be launched in one district or one division consisting of 4 to 5 districts in the pilot phase. The contractual duration is expected to be three years.
The solution would be completely scalable. Hence, the solution could be rolled out in other districts/divisions, ultimately to the whole state or even multiple states.
Scope of activities to be undertaken by Oglacs
Oglacs will be responsible for the following activities in lieu of deployment of the proposed engineering solution:
- Gathering of beneficiary data and process information.
- Printing of & Generation of SIO.
- Software Application Development and Systems Integration
- Data Center setup and application deployment on servers.
- Hosting and web services, software maintenance & bug fixing
- Maintenance, Operations and Project Management Services
- Fulfilling Service Level Agreement and achieving Key Performance Indicators
Provisions required from the government
Oglacs expects the government to provide the following for the deployment of the proposed solution:
- Provide clear sites and required infrastructure.
- Provide access to key sites and officials for information gathering.
- Permissions and access from government agencies when required.
- Ensure Physical Security and Safety of personnel and assets.
- Process related information including manual processes.
- Information on government rules and regulations.
- Information natural to the deployment and operation of the solution.
Apart from these, the following infrastructure would be required for the establishment of data center:
- At least 4 x 5 mtrs empty room within the District Collectorate or District Supply Office with tiled floor, false ceiling, electrical switches and points, painted walls and metallic gate.
- Electricity connection with generator backup.
- Leased optical/other line 4 mbps for internet connectivity.
Deployment Schedule
The following time-line is proposed for the deployment of the solution in one district or one division:
Gathering of Data 2 Weeks
Establishment of Data Center 2 Weeks
Delivery of services After 1month till contract
Main Business Objectives and Key Performance Indicators
During the pilot run of the project, the government/department may on its own conduct public surveys to confirm the outcome of the project. However, the actual cost-effectiveness of the solution will be analyzed both objectively and subjectively in terms of Main Business Objectives or MBOs and Key Performance Indicators or KPIs.
- Electronic storage and maintenance of records
- All grain movement must be recorded online
- All grain movement reports must be available online
- Portal must be up and accessible 24 hrs a day
- Reduction in theft and diversion of grains
- Grain Theft reduction targets must be met
- Grain diversion reduction targets must be met
- Improvement in grain distribution to consumers and FPS
- Consumer offtake of subsidized grain through PDS must increase
- FPS offtake of grains from SFC must increase
- Improvement in efficiency of the process
- Grain movement from FCI to SFC warehouses must be smooth with less incidents of theft
- FPS must not report distribution problems
- Enhancement in the Quality of Service (QoS)
- Consumer grievances must be addressed in reasonable amount of time
- Targets must be met for resolving consumer complaints in terms of number and time
Copyright Notice
Copyright (C) Oglacs Software Private Limited. All Rights Reserved.
This is a company confidential document and no part of this publication may be reproduced, stored in a retrieval system, or transmitted, in any form or by any means, electronic, mechanical, photocopying, recording or otherwise, without the prior permission of the copyright owners.